MOLD FLOW ANALYSIS
What is Mold Flow Analysis?
Mold flow analysis (MFA) software simulates the flow of plastic, which allows you to elevate part and mold design to create products of impeccable quality, it helps to reduce manufacturing defects. Like other simulation software, MFA gives you a virtual sneak peek into how your material of choice will fill the mold's cavities and offers a head's up on potential problem spots. The benefit is obvious, right? Simulating the process digitally means you can make changes on desigin stage. This one thing is a big cost savings, not to mention a time saver as well.
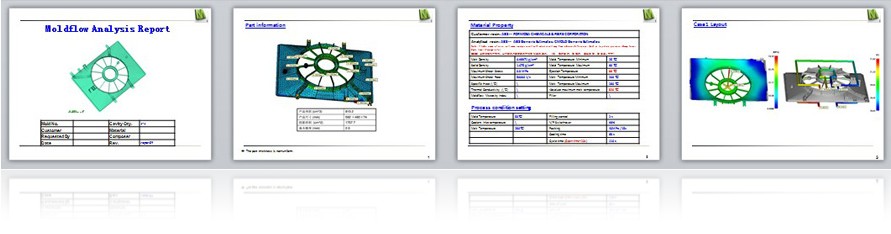
When Should Mold Flow Analysis be Used?
In case it wasn't clear, MFA is conducted before tooling production launches. (It wouldn't make much sense to use it afterward!) Using a selected gate location and material properties, the software is able to predict how the part will fill during molding. Different data points can be assessed, including pressure, fill time and melt temperature. Doing so allows for optimization of the process before tool manufacturing ever begins.
Is Analysis Necessary for Every Application?
The short answer: not necessarily. The following factors can help you decide whether MFA should be used for your application:
PRODUCT GEOMETRY
The more complex the product geometry, the more benefit you'll receive from MFA. Why? When the product's design is more intricate, the flow is less predictable. It's easier to predict how a simple mold design would fill, for example.
TOLERANCE REQUIREMENTS
Tight tolerances are an anathema to plastic injection mold designers anyway. Software that can analyse and demonstrate whether a product will meet spec prior to cutting a tool is a godsend.
PROJECT SCOPE
Clearly a project would have to meet certain financial requirements to warrant the investment of resources — time, software and talent — to run the tests.
UNUSUAL MATERIALS
Engineers know the fill patterns of standard materials but others — especially materials that include fillers — benefit from up-front analysis.
Mold flow analysis can provide you following benefits:
Moldflow Filling Analysis
- Optimize gating
- Optimize runner system
- Predict fill pattern
- Predict injection pressure
- Determine clamp tonnage
- Predict temperatures
- Visualize shear rate
- Visualize shear stress
- Determine fiber orientation
- Predict volumetric shrinkage
- Predict sink
- Determine venting
- Avoid air traps
- Locate weld (knit) lines
- Develop optimum ram-speed profile
Moldflow Cooling Analysis
- Find hot spots
- Calculate time to freeze
- Visualize uneven cooling across core and cavity
- Determine uneven cooling between core and cavity
- Define required coolant flow rates
- Measure pressure drop in cooling system
- Determine (and reduce) cycle time
- Optimize the cooling layout
Moldflow Packing Analysis
- Calculate proper packing pressure
- Define optimum packing profile
Moldflow Warpage Analysis
- Predict warpage
- Find cause of warpage
- Determine warpage due to orientation
- Predict warpage due to differential cooling
- Understand warpage due to differential shrinkage
Moldflow Gas-Assist Analysis
- Determine optimized gas channel layout
- Predict gas penetration
- See gas permeation
- Predict skin/core ratio Establish required gas pressure
- Define optimized gas pressure profile
- Refine spillover design
Moldflow Co-Injection Analysis
- Compute skin/core ratio
- Calculate skin/core distribution
- Establish switch over points for skin/core (A-B)
- Establish switch over points skin/core/skin (A-B-A)
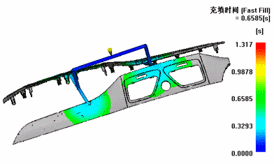
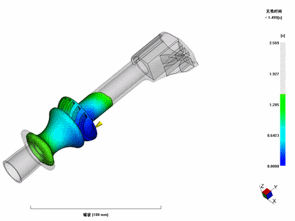