PLASTIC MOLD DESIGN
Main Stages of Plastic Mold Design
Stage 1: Manufacturability and Feasibility
In this initial stage, design engineers, tooling engineers, materials engineers and manufacturing engineers work together to determine product specifications, mold component functionality, mold materials, operational constraints, and any needed product enhancements and improvements. The team especially looks for any potential problems in part geometry or tolerance that might result in poor steel conditions or require special tooling features such as lifters, slides, and threading/unthreading. The physical and chemical properties of the selected resin are also evaluated so that the proper mold steel can be selected and mold cooling be reviewed. Mold flow evaluation is also undertaken to determine the best type of gate and gate locations, in addition to determining proper vent locations.
Manufacturability review includes confirmation of standard plastic design practices and incorporation of tooling details to create the most robust design possible. Tooling specifications and tooling sources are finalized and purchased component sources qualified. A comprehensive process failure mode effects analysis (PFMEA) is also completed.
Stage 2: Design
Preliminary 2D and 3D design models are constructed to determine mold sides and steel sizes. Once these are reviewed and approved, the detailed design is finalized.
Stage 3: Final Design Specifications
The tool builder is given the tool design specifications for mold construction. Final adjustments and modifications are done in-house, with special attention given to manufacturability and critical dimensional requirements.
Stage 4: Bring the Tool In-House for the Initial Sample
A molding process is established that is acceptable to the manufacturing department. Processing parameters are recommended and established. Initial sampling using scientific molding practices is carried out; cavity pressure transducers in the mold accurately determine the filling profile over time. Sample parts are qualified.
Stage 5: Make Any Final Tool Corrections
Any needed process adjustments are made as required. Tool construction is verified and the process is detailed and documented so it can be used in the future with minimal setup time. Perfect parts are resampled and submitted to the customer. After final approval is obtained from the customer, the production process is launched.
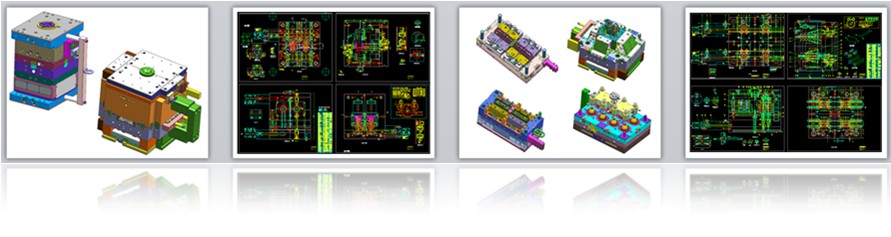
High quality mold is based on excellent Plastic Mold Design, we have extensive experience in building different types of molds like:
◆ 2K Mold
◆ Over Mold
◆ Insert Mold
◆ Stack Mold
◆ Hot runner Mold
◆ Cold runner Mold
◆ Unscrewing Mold
◆ Prototype Mold
We will offer steel certification and heated treatment certification for full-hardened steel. Below are some of our steel suppliers as Uddeholm, ASSAB , LKM, BÖHLER, Gröditz,SSAB, FINKEL,SCHMOLZ-BICKENBACH,DAIDO, HITACHI .......
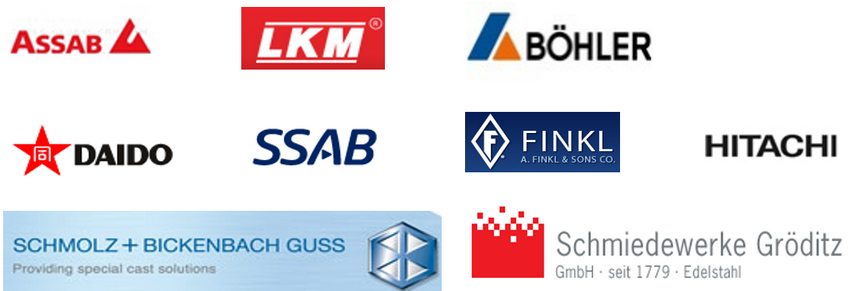
Almost all the molds are for overseas customers, so we choose mold components that easy to buy in different overseas country. Below are some of our components suppliers as HASCO, DME, Meusburger, DAIDO, CUMSA, LKM, MISUMI, PUNCH, PARKER, MERKEL, HP SYSTEM, Stäubli......
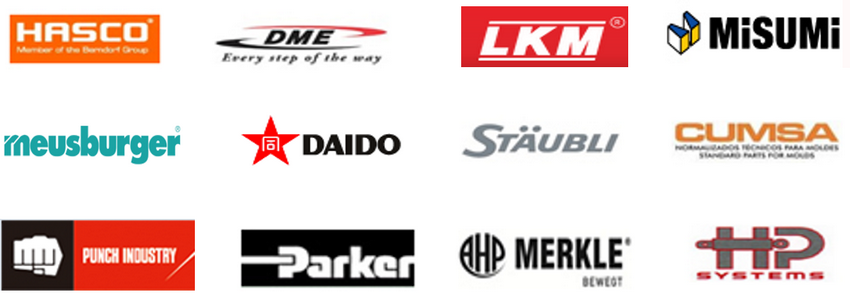
We know hot runner system is very important for the mold, so we know which kind of mold need which kind of hot runner system. Below are some of our hot runner system suppliers as HRS, HUSKY, MOLDMASER, INCOE, SYNVENTIVE, YUDO, männer, GÜNTHER, THERMOPLAY, MASTIP, HOTSYS.......
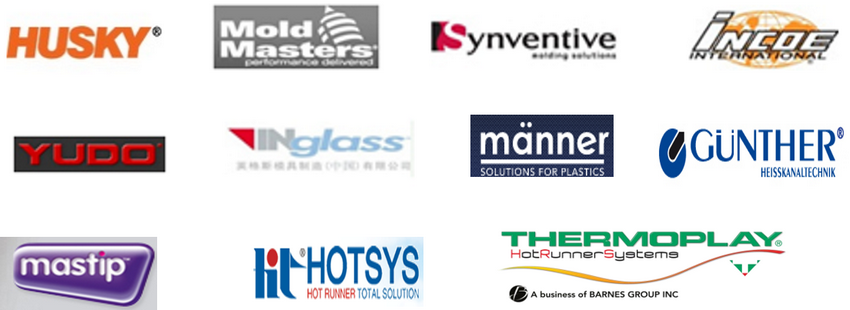
We partner with the customer through all stages of design, material selection, Plastic Mold Design, testing, processing, and production. RCH Plastic is expert in converting metal components to Plastic Products parts allow for our customers to reduce overall product cost and weight while improving performance.
Plastic Mold Design & tooling constitute a major part of the design contracts we undertake. We are a group of individuals who share tremendous passion for Plastic mold design & for all things related to bringing any new product to life. Nothing gives us as immense pride as watching our designed/developed product performing to excellence.
RCH Plastic has injection mold design specialists with over 15 years of experience and expertise in the industry. We have designed hundreds of molds, including automotive, medical, home appliances, optical, and office equipment.
We strictly adhere to DFM, moldflow, 2D/3D mold design, and other processes to meet the precise client’s requirements. With a vast background and knowledge, we are experts in providing injection mold design services and other tooling requirements. We manufacture injection molds upon your request at competitive prices.
Injection Molding Quality You Can Trust
As a leading manufacturer of injection mold design and products, we ensure to provide our customers with high quality at fair prices. We have a proven track record of catering to various sectors, including industrial, automotive, telecommunications, pharmaceuticals, consumer electronics, and more.
We excel in custom plastic injection molding in our own facilities. We use a dual business model to provide lower costs, the best quality, and no headaches. For every molding project, we call out an internal meeting to determine the part layout, runner design, gating way, ejection method, and cooling layout. We assure full commitment to top-of-the-line mold quality standards and on-time delivery of parts.
Custom Injection Molded Plastic Parts
RCH Plastic is your go-to source for mold design, plastic injection molding, and custom injection molding. We have the capability and capacity to produce 40-50 plastic injection molds per month.
Our mission is to be a professional, creative, and trustworthy mold maker and plastic injection mold manufacturer. We ensure zero defects and use the best techniques to produce top-level injection mold designs.
We offer:
• Thorough evaluation of your injection parts design so you can avoid production problems. • Redesign your parts to ensure the manufacturer optimal design
• On-the-ground plastic injection mold to assure clear communication and effective production cycle. • Expert mold design in China following international manufacturing standards
• Progress reports of your injection molding projects
Reach Out to RCH Plastic for Injection Molding
RCH Plastic has years of experience in injection molding service and deeply understands customer concerns. We ensure the protection of intellectual property, adherence to original product design, a high level of service, and quality injection molds. We give equal attention to each process to ensure effective injection molding and no chances of mistakes. Needless to say, molds produced with expert assistance in high-tech facilities will ensure to meet the levels of quality you’re expecting.
To request a quote, don’t hesitate to contact us!